href = "jpg/construction4.jpg">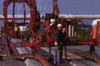 The rails are placed on the ties.
Note how flexible they are. Photo: C. Recoura / LVDR
The sections of rail are welded together using thermite. Conventional
welding (using some type of flame) does not work well on large metal
pieces such as rail, since the heat is conducted away too quickly.
Thermite is better suited to this job. It is a mix of aluminum powder
and rust (iron oxide) powder, which reacts to produce iron, aluminum
oxide, and a very large amount of heat. This last property is what
makes it ideal to join pieces of rail. Before the rail is joined, its
length must be adjusted very accurately. This ensures that the
thermal stresses in the rail after it is joined into one continuous
piece do not exceed certain limits, resulting in lateral kinks (in hot
weather) or breaks (in cold weather). The joining operation is
performed by an aluminothermic welding machine which is equipped with
a rail saw, a weld shear and a grinder. When the thermite welding
process is complete, the weld is ground down to the profile of the
rail, resulting in a seamless connection between adjoining sections.
Thermal stresses in the rail due to varying ambient temperatures are
absorbed without longitudinal strain, except near bridges where an
expansion joint is sometimes used.
The next
step consists of stuffing a deep bed of ballast underneath the new track.
The ballast arrives in a train of hopper cars pulled by one or two
diesels. Handling this train is challenging, since the ballast must be
spread as evenly as possible. If the train stops, ballast can pile over
the rails and derail it. A first layer of ballast is dumped directly onto
the track, and a tamping-lining-levelling machine, riding on the rails,
forces the stones underneath the ties. Each pass of this machine can
raise the level of the track by 8 cm (3 inches), so several passes of
ballasting and of the machine are needed to build up a layer of ballast at
least 32 cm (1 foot) think under the ties. The ballast is also piled
thick on each side of the track for lateral stability. The machine
performs the initial alignment of the track. Next, a ballast regulator
distributes the ballast evenly. Finally, a dynamic vibrator machine
shakes the track to perform the final tamping, effectively simulating the
passing of 2500 axles.
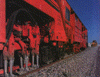 The tamping machine.
Photo: C. Recoura / LVDR 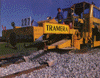
The ballast regulator. Photo: C. Recoura / LVDR
Now that
the first track is almost complete, work begins on the adjacent track.
This time, however, it is not necessary to lay a temporary track. Trains
running on the first track bring the ties, and then the rail, which is
unloaded directly onto the ties by dispensing arms that swing out to the
proper alignment. The Nabla fasteners are secured, and the ballast is
stuffed under the track as before.
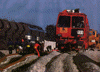 Left: a ballast train
arrives behind two 67000-class diesels. Middle: work on the second
track. Right: the tamper and regulator at work on the first track.
Photo: C Recoura / LVDR
The two
tracks are now essentially complete, but the work on the line is not
finished. The catenary masts need to be erected, and the wire strung on
them. Catenary installation is not complicated; it will suffice to give a
brief summary of specifications. The steel masts are I-beams, placed in a
concrete foundation up to 63 m (206 ft) apart. The supports are mounted
on glass insulators. The carrier wire is bronze, 65 mm^2 cross section,
14 kN (3100 lb) tension. The stitch wire is bronze, 15 m (49 ft) long, 35
mm^2 cross section, The droppers are 5 mm stranded copper cable. The
contact wire is hard drawn copper, 120 mm^2, flat section on the contact
side, 14 kN tension. The maximum depth of the catenary (distance between
carrier and contact wires) is 1.4 m (4 feet). The contact wire can rise a
maximum of 240 mm (9 inches) but the normal vertical displacement does not
exceed 120 mm (4 inches).
Now that the catenary is complete, the track is given final alignment
adjustments down to millimeter tolerances. The ballast is then blown to
remove smaller gravel fragments and dust, which might be kicked up by
trains. This step is especially important on high speed tracks, since the
blast of a passing train is strong. Finally, TGV trains are tested on the
line at gradually increasing speeds. The track is qualified at speeds
slightly higher than will be used in everyday operations (typically 350
km/h, or 212 mph), before being opened to commercial service.
See more pictures of track construction
here in TGVweb or on the
LGV Méditeranée
official web site.
Last Update: February 2000
|
|
|
|
|
|
|